Ergoseal Meets and Exceeds Requirements for Defense Industry Client
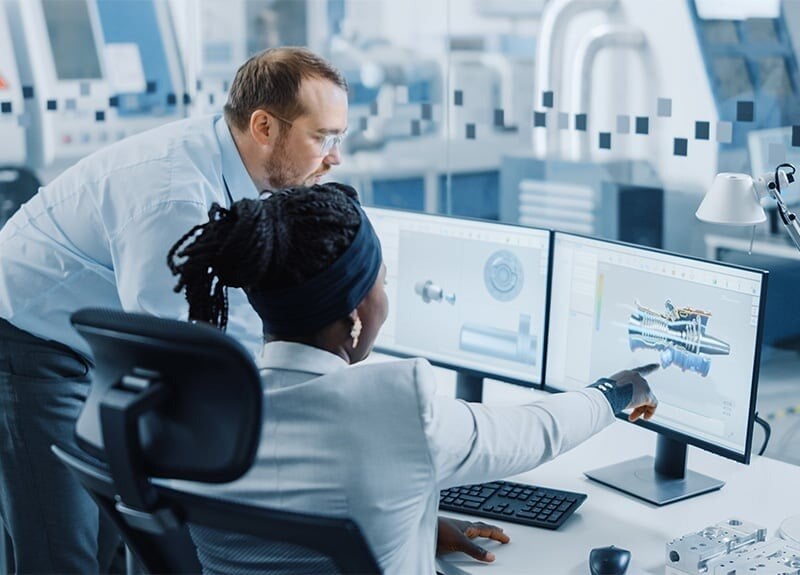
Overview
In mid-October 2019, one of Ergoseal’s defense industry customers initiated a new project to retrofit an existing seal that Ergoseal provided to them. Now, they needed it for a new coolant pump application.
While Ergoseal also offers in-house testing for a range of validation strategies,
in this case Ergoseal was able to apply its simulation capabilities rapidly and cost-effectively toward customization and optimization of an existing seal to meet customer requirements.
Engineering a 75% reduction in leakage
In mid-January 2021, the customer’s project had progressed to include not only more demanding operating conditions, but also more stringent leakage requirements—instead of the existing 1 cubic centimeter per hour leakage limit, the customer required a more stringent 0.25 cubic centimeters per hour limit, or a 75% reduction, all within the same form factor and approximate price structure.
Ergoseal accepted the challenge and guided the customer through its Feasibility Study and Advanced Verification (FSAV) process.
Modify and optimize legacy seal to new specificatons
First, the Ergoseal team ensured clarity and alignment with the customer’s needs and constraints. Then, they leveraged their experience and multiple mechanical-seal-specific FEA simulation tools to modify and verify changes to the existing legacy seal’s dimensions, materials, and mechanical behavior.
After several simulation iterations optimized for improved sealing and considering face seal design fundamentals such as seal balance ratio, face taper, and viscous shear, they submitted a design proposal and FSAV report predicting a 60–90% reduction in leakage flow rate. Based on this performance output in addition to various others including running torque, power consumption, wear rate, and estimated seal life, the customer approved the design and submitted an order for prototype test samples.
Exceeded expectations
After design plan release to production, in-process/post-process inspection, and shipment per Ergoseal’s AS9100D-certified quality system, Ergoseal diligently followed up with the customer to learn the prototype validation test results.
In mid-May 2021, when the customer had conclusive results that matched from redundant tests in parallel. They shared a leakage rate below 0.1 cubic centimeters per hour, which met and even exceeded the leakage requirement as well as validated Ergoseal’s simulation predictions.
While Ergoseal also offers in-house testing for a range of validation strategies, in this case Ergoseal was able to apply its simulation capabilities rapidly and cost-effectively toward customization and optimization of an existing seal to meet customer requirements.
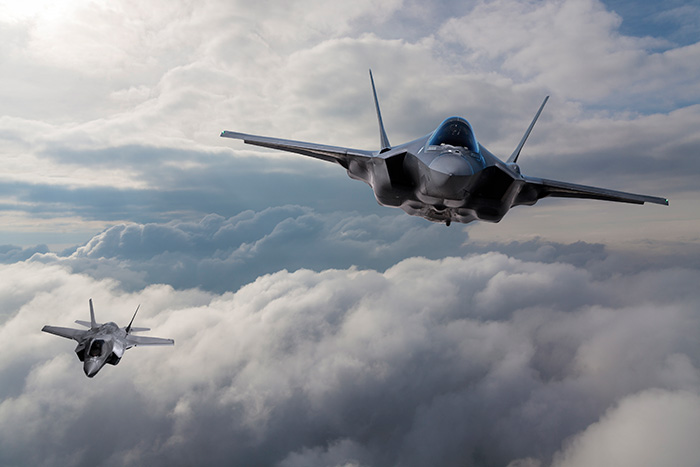
We would like to re-emphasize that the [custom seal] was a successful product.
It exceeded all of the requirements and expectations of low dynamic leakage and low power consumption with all the design benefits provided by a mechanical seal in a familiar package. We look forward to using this seal in our future designs.
Confidential ClientHave a project? Tell us how we can help.
Our seal design and engineering department have expertise in a wide variety of sealing solutions to help you find your perfect solution.